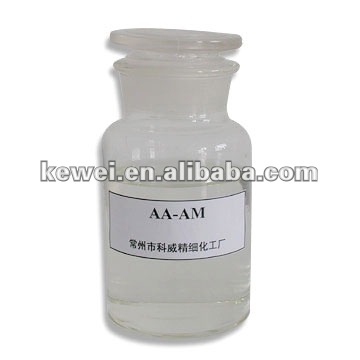
Nippon Shokubai Co. (Nisshoku; Osaka, Japan; http://www.shokubai.co.jp) is developing a process for making acrylic acid from glycerin directly obtained as a byproduct from biodiesel-fuel (BDF) production. In 2007, Nisshoku demonstrated, under a grant from the Research Institute of Innovative Technology for the Earth (Kyoto, Japan; http://www.rite.or.jp), a process that co-produces BDF and glycerin with 98% purity from vegetable-based biomass, such as palm oil. The company has produced 20 ton/yr of fatty acid methyl ester (FAME) with 99 mol% yield, and 2 ton/yr of glycerin at their Tsukuba Research Laboratory. Now, it plans to use this glycerin to make acrylic acid, a precursor for making plastics, coatings, adhesives and elastomers.
In the process, glycerin is dehydrated over a new, supported acidic/basic catalyst to form acrolein, which is then oxidized into acrylic acid using the company’s proprietary oxidation catalyst. In conventional routes, acrolein is made from propylene oxide by a two-step process.

Nisshoku is now optimizing the glycerin dehydration step at the laboratory scale, aiming to produce acrolein with a yield of 80–90 mol%, and is also investing ¥2 billion ($20 million) over 2009–2010 for a pilot facility, with support from the New Energy and Industrial Technology Development Organization (Kawasaki, Japan). The company plans to finish bench-scale test and pilot-facility design this year, and begin installation and operation of the pilot facility at its Himehi site for demonstrating acrolein production in 2010. The basic design of a commercial plant is planned for 2011, with a study for commercialization by 2012.