Monday, October 29, 2012
A commercial algae farming for CO2 recovery

Advanced Algal Technologies (Sydney, Australia; www.advancedalgal.com) has signed a $100-million deal with Fuzhou Xiangli Enterprise Management Consulting (Fuzhou, China) — an LED-lighting manufacturer for a license to build 500 algal-farming conveyor modular units per year. Traditionally, algae have been grown either in open ponds, or in bioreactors.
In the patented system, developed by Advanced Algal Technologies, the algae are grown on a fabric inside an insulated building, within a precisely controlled environment. The company said the system allows maximum algae yield. Artificial photosynthesis Scientists at Panasonic Corp. (Osaka, Japan; www.panasonic.com) have developed an arti¬ cial photosynthesis system that utilizes sunlight to convert CO2 to organic materials (mainly formic acid) at what is said to be the highest efficiency yet achieved (0.2%). Cheaper chemicals from algae, farms & forest may be possible to a Lux Research (Boston, Mass.; www.luxresearchinc.com) report.
Currently, the high cost of capital and operations limit bio-based materials and chemicals to a few facilities. Bio-based materials and chemicals manufacturers need syngas [synthesis gas] and sugar to fuel their growth. Lux Research analysts studied cost drivers in gasification, enzymatic hydrolysis of cellulose and algae cultivation to find opportunities where new technologies can turn them to profit.
Algae remains a costintensive loser. In Lux Research’s model, algae cultivation yields a 48% loss, calling into question its long-term prospects. The problem lies in the high capital costs for growing algae at industrial scale. Syngas fermentation has great new product potential.
Sunday, October 28, 2012
Texas-based refinery has a long history
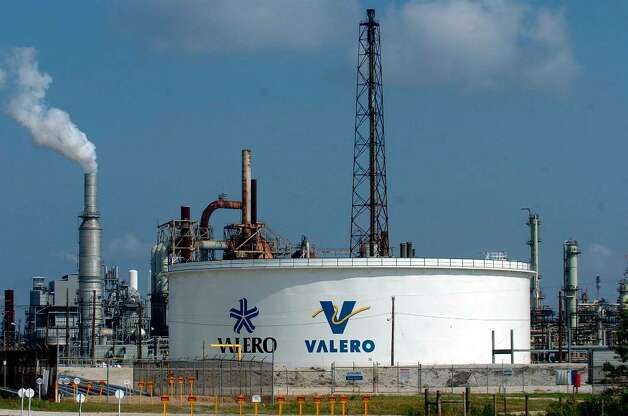
The Valero Port Arthur Refinery was commissioned in 1901 and has had many process additions and improvements throughout its history. In 2001, nearly $850 million was invested in a delayed coker and hydrocracker to enable the plant to run heavy and sour crude.
![]() |
The Valero refinery near Port Arthur, Texas |
Other investments include the recent expansion of the coker to 95,000 bpd from 85,000 bpd. The most recent expansion of the crude and vacuum units has increased the refinery’s ability to process lower-cost, heavy sour crude oil and increased throughput capacity to 310,000 bpd. The refinery is strategically located on the Texas Gulf Coast, approximately 90 miles east of Houston. The refinery’s location accommodates its extensive logistics system, which includes access to Gulf Coast water-borne crude oil via the refinery docks or through the Nederland, Texas, terminals of Sun or Oil Tanking. The milestones of this refinery are:
- Commissioned in 1901, with many upgrades since then
- One of four refineries acquired in the purchase of Premcor in 2005
- Total throughput capacity of 310,000 bpd
- Has ability to process 100% sour crude oil, of which up to 80% can be heavy sour crude oil
- Production includes conventional conventional, premium and reformulated gasoline before oxygenate blending, as well as diesel, jet fuel, petrochemicals, petroleum coke and sulfur
- Strategically located on 4,000 acres on the Port Arthur Ship Channel
- Crude oil received from the Valero dock or by pipeline
- The Port Neches dock’s crude oil receipts transferred by the Valeroowned Lucas pump station, located about 13 miles from the refinery
- Refinery production distributed into the Colonial Pipeline, Explorer Pipeline and Teppco Pipeline or across the refinery docks into ships or barges
- Employs approximately 820 individuals.
Awards and honors.
This refinery is one of only two Texas refineries Environmental Management System certified. It is TCEQ Clean Texas Program Bronze member and has received EPA National Partnership for Environmental Priorities, 2008 Pollution Prevention Achievement Award. This refinery has attained more than 1 million hours without a lost-time injury.
Future bright for molybdenum

Roskill recently released a market outlook on molybdenum. The company expects that molybdenum growth rates will exceed global GDP rates to 2016. Global demand for molybdenum bounced back from the impact of the global economic downturn, growing by just over 11% in 2010 and a further 9% in 2011, according to the report. China now accounts for around 31% of global molybdenum demand and its growth rates continue to outpace those in other countries. While global demand for molybdenum is forecast to grow at an average of 4.6% per year to 2016, Chinese demand is forecast to increase by 7.5% per year. The principal engines of growth will be increased use of stainless and other steels containing molybdenum in process, power and desalination plants, in oil and gas production and distribution and in motor vehicle components. The greater use of molybdenum steels and high performance alloys and catalysts, combined with robust growth in the economies of the BRIC countries and other countries in Asia and South America, will ensure growing future demand for molybdenum.
![]() |
molybdenum. Courtesy of wikipedia |
Mine capacity sufficient to meet demand until 2015. Primary molybdenum mines were the first to respond to the recovery in demand in 2010, but, in 2011,growth in output of byproduct molybdenum from copper mines outpaced growth from primary mines. In 2012, mine capacity is sufficient to meet demand and supply is likely to show a surplus over the next three years. Roskill lists some 60 new projects and expansions that could potentially produce molybdenum, yielding an additional 240 ktpy, indicating that longterm mine supply is assured. Around 33% of new projects identified in 2012 are located in North America, 28% in Central and South America and 10% in China. In the next two years, byproduct output is likely to grow at a higher rate, but, from 2014 on, new Chinese molybdenum-only projects will redress the balance. In the past, insufficient roasting capacity has resulted in a bottleneck, but additional capacity has been installed and further additions are under construction in Chile,China and the US by Codelco, Molymet,China Molybdenum and JDC.
Subscribe to:
Posts (Atom)