Dear Fellow, When I Searching on site about improved Feed system, i had found something that maybe you would to see. Please read this up. And tell me about your opinions.
SNC-Lavalin Calgary has successfully incorporated ASD OptiPlant into the EDS Phase of the North West Upgrader Project and has achieved a 50% savings in piping design hours over conventional practices of applying a 3D detail design tool for the work to date. ASD Optiplant helped to verify and optimize the plot plan to produce a quality conceptual design with fewer resources.
PROBLEM Defined by SNC-LAVALIN
Phil Stephenson, Manager Plant Layout & Piping, at SNC-Lavalin Calgary, defined the problems in FEED work. (Similar issues exist with lump-sum bid efforts.) Prior to utilizing ASD’s solution, SNC-Lavalin’s options were to use any combination of manual sketching, 2D piping packages and 3D detailed design tools. All of these options required a large number of designers to work the layout while P&ID's were still under development. To keep up with the volume of work and still maintain the expected progress, the designers were not able to focus on the most basic functions of the group, namely to work several options of the plant layout for optimal results. The alternate tools are labor intensive, therefore the quality of the layout would suffer as too many designers were involved. It was also a struggle to keep up with the P&ID development. When moving into detailed design, there would be a significant amount of rework to bring the models to the level of quality required because the models built with detailed design tools were based on incomplete Reference Databases (RDB's).
SNC-LAVALIN OBJECTIVES
- Improve the quality of FEED layout by using fewer and more senior layout designers
- Allow the plant layout designers to focus on what they do best and not worry about the details of a detailed 3D model - SIMPLIFY
- Improve accuracy of Material Take-offs (MTO's) and be less reliant on factors and allowances
- Flexibility to work more than one plant layout option and provide MTO comparisons
- Complete FEED with a layout and MTO which accurately reflect the P&ID's issued for FEED
- Make use of FEED deliverables in detailed engineering with less rework, knowing the layout has been optimized
- Avoid the use of detailed engineering tools in FEED
- Avoid the need to setup a client-specific material database and all the setup associated with detailed 3D design tools
- Avoid the need to source large numbers of designers for a short period of time with the required FEED skills
- Change the mindset that an MTO from a detailed 3D design tool is somehow more accurate.
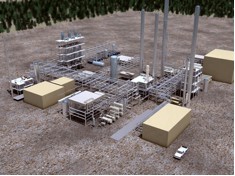
SCOPE
The North West Upgrader Project includes 18 units, 2000 items of equipment and 6000 lines. ASD’s OptiPlant software is utilized for plot plan development including: equipment modeling, structures modeling and automatic 3D interference free pipe routing. Accurate piping MTO’s and drawings for the units are automatically extracted by line-number and specification-driven totals. Major inline components such as control stations are placed at either user defined locations or selected automatically by the pipe router.
Each unit is modeled as a separate area or project and Rule-based Nozzles provided by Optiplant is used to assign Start and End point location for the lines. The lines are routed using a batch process and each area completed to date has an interference-free run of over 95%. The balance of lines are routed using the interactive online routing feature.
One of the major benefits of Optiplant noted during this process is efficient change management. During the course of the project, the plot plans and P&ID’s have been updated several times. These modifications are incorporated in the OptiPlant model rapidly and revised piping MTO’s are produced spending very few additional hours.
Each unit is modeled as a separate area or project and Rule-based Nozzles provided by Optiplant is used to assign Start and End point location for the lines. The lines are routed using a batch process and each area completed to date has an interference-free run of over 95%. The balance of lines are routed using the interactive online routing feature.
One of the major benefits of Optiplant noted during this process is efficient change management. During the course of the project, the plot plans and P&ID’s have been updated several times. These modifications are incorporated in the OptiPlant model rapidly and revised piping MTO’s are produced spending very few additional hours.
ASD’s Pipe Support Optimizer (PSO) was used to automatically locate supports and analyze the stress critical lines. The resulting stress reports and stress isometrics were validated within CAESAR on selected lines. By using PSO, the stress group was able to analyze 60% of the stress critical lines in half the normal time and with little re-engineering.
The project team continues to successfully demonstrated the application benefits of ASD’s FEED solution to automate the conventional work process as well as its’ cost-effectiveness with respect to design hours and material costs. If this effort was to be completed in a detail design system, the manhours required would have been at least 2 times greater and the changes could not have been incorporated.
ASD Optimized Plant Design (OPDTM) SOLUTIONS
OPTIPLANT CONFIGURATOR™
Knowledge based engineering application for optimizing plant layouts by automating 3D Plant Modeling and Pipe Routing. The OptiPlant work process involves integration with Front End Process engineering tools and costing tools to reduce FEED time, generate MTO’s and produce realistic plant walkthroughs in early stage of plant design. The quick 3D modeling of plant equipments & structures and basic pipe routing features available in the tool make it best for Proposal Engineering, Bidding and FEED stages of Plant Design.
PIPE SUPPORT DESIGNER™
It is an integrated piping stress analysis, support optimization and design tool. It provides automatic feasible pipe support Location and Type identification & support optimization along the piping route. It carries out complete piping stress analysis for thermal, gravitational and seismic loads along with code compliance checking.
“The piping discipline committed to use the Optiplant software for plot development and MTO’s. They successfully produced the deliverables to support FEED.
No comments:
Write comments